Lean office management
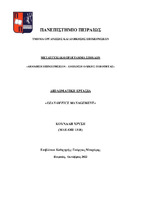
Προβολή/ Άνοιγμα
Λέξεις κλειδιά
Απόβλητα ; Αξία ; Πόροι ; Τομέας υπηρεσιών ; Lean managementΠερίληψη
Το Lean Management έχει εφαρμοστεί με επιτυχία από εταιρείες σε όλο τον κόσμο, στο παρελθόν κυρίως σε λειτουργίες παραγωγής και κατασκευής. Τα τελευταία χρόνια έχει αυξηθεί το ενδιαφέρον για την ευρύτερη εφαρμογή του Lean Management στον τομέα των υπηρεσιών. Το Lean Management επί του πρακτέου περιγράφει ένα σύνολο αρχών και μεθόδων διαχείρισης των υπηρεσιών σχετικά με τη σχέση μεταξύ «αξίας» και «κόστους» στους οργανισμούς (Stone 2012). Ως κόστος/δαπάνη μπορεί να οριστεί «κάθε ανθρώπινη δραστηριότητα που απορροφά πόρους αλλά δεν δημιουργεί αξία και κέρδος» (Womack & Jones 1996) και ως αξία-κέρδος ορίζεται «η ικανότητα που παρέχεται σε έναν πελάτη την κατάλληλη στιγμή να επιλέξει την σωστή παρεχόμενη υπηρεσία, όπως ορίζεται σε κάθε περίπτωση από τον πελάτη», (Womack & Jones 1996). Παραδείγματα κόστους είναι τα ελαττώματα στις υπηρεσίες όπως η επιπλέον επεξεργασία, η απογραφή, η κίνηση, η υπερπαραγωγή, η μεταφορά και η αναμονή (Ohno 1988). Το πιο διάσημο παράδειγμα για την εφαρμογή της Lean Management είναι η Toyota, η οποία κατατάχθηκε ως ο νούμερο 1 κατασκευαστής στις παγκόσμιες παραδόσεις αυτοκινήτων το 2013 (Bloomberg 2014). Το Lean Management βρίσκεται ψηλά στην ατζέντα διαφόρων συμβουλευτικών υπηρεσιών (Bain & Company 2014; McKinsey & Company 2014; The Boston Consulting Ομάδα 2014). Εκτός από την επιτυχία του στις παραγωγικές/κατασκευαστικές λειτουργίες, αυξήθηκε το ενδιαφέρον για διερεύνηση της ευρύτερης εφαρμογής του Lean Management και σε μη παραγωγικές/κατασκευαστικές λειτουργίες (Arlbjørn & Freytag 2013, Stone 2012). Προκειμένου να κατηγοριοποιηθεί και να κατανοηθεί η εξέλιξη του Lean Management τις τελευταίες δεκαετίες, έχει πραγματοποιηθεί μια ευρεία διεπιστημονική έρευνα (Arlbjørn & Freytag 2013; Hines, Holweg, & Rich 2004; Stone 2012). Πλέον, εφαρμόζεται συχνά στον τομέα των υπηρεσιών, στον οποίο αποφέρει εξίσου σημαντικά οφέλη.